How Predictive Maintenance and Thermal Imaging can ensure system efficiencies and minimise plant downtime. Heat is a form of energy, so where heat is lost, energy is lost. With 2020 energy targets looming, energy efficient grants are becoming more prevalent and companies are becoming more and more focused on green and sustainability initiatives.
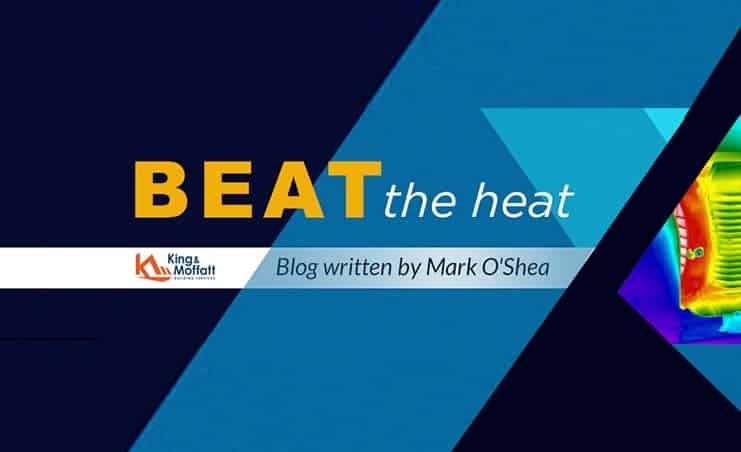
Unfortunately, a lot of companies are overlooking one of the most lucrative opportunities for energy savings – predictive maintenance in the form of infrared thermography.
Infrared thermography is a non-destructive, predictive maintenance technique that can be used to monitor the thermal signatures of plant machinery, electrical apparatus and building systems without disrupting normal operations.
Regular thermographic inspections can be an extremely effective tool to optimise equipment and system efficiencies. They help diagnose existing or potential failures of electrical, mechanical, refractory and building envelope related systems, saving your facility from the expense and inconvenience of significant or catastrophic equipment failure.
Studies have shown that companies can cut energy consumption at a plant by 10%, while also preventing possible health and safety issues like fire hazard. Many industrial, high-rise and commercial fires are caused by faulty electrical components, which result in costly downtime, lost production, equipment replacement costs, injury or, at worst, loss of human life.
Infrared thermography provides non-destructive detection of potential “hot spots” and allows for planned monitoring of electrical apparatus and scheduling for preventive maintenance repairs before catastrophic failure occurs. The old saying illustrates a “picture paints a thousand words”. King & Moffatt Building Services comprehensive thermal imaging surveys will aid you to identify potential and existing problems and hazards before they become visible to the human eye.